Theo đánh giá của Hiệp hội công nghiệp môi trường Việt Nam, ngành Thép có tiềm năng tiết kiệm năng lượng lên tới 20-30% tùy theo công nghệ sản xuất. Con số này cho thấy cơ hội tiết kiệm năng lượng của ngành Thép là rất lớn, nhưng để đạt được mức tiết kiệm năng lượng như kỳ vọng là cả một quá trình, với rất nhiều khó khăn và thách thức, cần những định hướng và giải pháp quyết liệt, đặc biệt là việc đổi mới và lựa chọn công nghệ phù hợp với tình hình phát triển của Việt Nam và xu hướng phát triển của ngành thép trên thế giới.
Hiện trạng công nghệ ngành Thép
Ngày nay, mặc dù nhiều loại vật liệu đã được nghiên cứu, sản xuất và ứng dụng như chất dẻo, thuỷ tinh, ceramic... nhưng sắt thép vẫn giữ được vai trò trọng yếu trong các ngành chế tạo máy, xây dựng, giao thông vận tải, nông nghiệp, năng lượng, sản xuất hàng gia dụng, y tế và an ninh quốc phòng.
Sản lượng thép trên thế giới đã và vẫn đang tăng trưởng rất nhanh, giai đoạn 2000-2005, tốc độ tăng bình quân 6,2%/năm; giai đoạn 2005-2010 là 4,5%/năm; giai đoạn 2010-2015 là 2,5%/năm và giai đoạn 2015 - 2017 là 2,1% (World steel in Figures 2018, World Steel Association).
Các công nghệ chính sản xuất phôi thép được thể hiện ở sơ đồ sau:
Trong đó, trên thế giới, sản lượng thép được sản xuất bằng công nghệ Lò chuyển (Basic Oxygen Furnace - BOF) chiếm tới 70%, công nghệ Lò điện hồ quang (Electric Arc Furnace - EAF) chỉ chiếm gần 28%, một số ít còn lại (khoảng 2%) được luyện bằng công nghệ Lò điện cảm ứng (Induction Furnace - IF).
Việt Nam hiện nay cũng đang sử dụng 3 công nghệ sản xuất thép như trên, nhưng ngược lại với thế giới. Theo thống kê của Hiệp Hội Thép Việt Nam tại thời điểm năm 2018, Việt Nam có tổng số 29 đơn vị sản xuất thép, trong đó có 5 đơn vị sử dụng BOF, 15 đơn vị sử dụng EAF và 8 đơn vị sử dụng IF. Tổng công suất thiết kế của các đơn vị là 18.500.000 tấn/năm, trong đó công suất thiết kế của các nhà máy lò BOF, EAF và IF lần lượt là 9.100.000 tấn/năm (chiếm 49,2%), 7.000.000 tấn/năm (chiếm 37,8%) và 2.400.000 tấn/năm (chiếm 13%).
Công nghệ BOF
Nguyên liệu chính đầu vào lò gồm gang (chủ yếu là gang lỏng), oxy và các phụ gia (vôi, dolomite,…). Thép phế cũng được sử dụng theo một tỷ lệ nhất định (10 - 15%) để làm nguội trong quá trình BOF. Để luyện thép cần nhiên liệu đốt lò cao (than, điện, dầu).
Sơ đồ công nghệ luyện thép lò chuyển BOF:
Theo số liệu của Hiệp hội Thép Việt Nam năm 2018, Việt Nam có 08 lò BOF, có dung lượng lò từ 20 đến 320 tấn/mẻ, chiếm 49,2% tổng công suất thiết kế. Sản lượng thép BOF năm 2017 đạt 4.025.000 tấn, chiếm 35% tổng sản lượng phôi thép của cả nước. Trong những năm tới, công nghệ BOF sẽ phát triển mạnh và trở thành công nghệ luyện thép chính ở nước ta.
a. Trình độ công nghệ
Theo kết quả điều tra khảo sát, hầu hết các lò chuyển luyện thép ở Việt Nam là loại nhỏ nhưng mới được xây dựng và đưa vào sản xuất từ sau năm 2010 nên đã đạt được các thông số kinh tế - kỹ thuật khá tiên tiến.
b. Sử dụng năng lượng
Đối với luyện thép bằng lò chuyển chỉ sử dụng oxy và điện để vận hành các thiết bị phụ trợ. Vì vậy, tiêu hao năng lượng của khâu công nghệ này rất ít, chỉ khoảng 200 MJ/tấn. Đối với các lò có dung tích trên 100 tấn còn có thể phát thêm điện năng nếu thực hiện thu hồi nhiệt khí thải để phát điện.
Tóm lại, qua khảo sát cho thấy, các cơ sở luyện thép công nghệ BOF ở nước ta do mới xây dựng trong những năm gần đây nên có các chỉ tiêu về suất tiêu hao năng lượng, nguyên liệu, mức độ phát thải cũng như các chỉ số kỹ thật khác đạt trình độ tiên tiến. Vấn đề còn lại chỉ là cần duy trì chế độ vận hành, bảo trì, bảo dưỡng nghiêm ngặt. Nếu thực hiện tốt điều này, công nghệ BOF ở nước ta có thể so sánh được với trình độ công nghệ tiên tiến của thế giới.
Công nghệ EAF
Khác với công nghệ BOF, trong công nghệ EAF, nguyên liệu chính cho lò là thép phế. Thép phế là nguồn sắt tương đối tinh khiết so với quặng sắt mặc dù cần lưu ý rằng các tạp chất có thể có như kẽm (phế thép mạ kẽm), thiếc (thép mạ thiếc) và các nguyên tố khác (các phế thép hợp kim). Nhờ sử dụng thép phế nên công nghệ sản xuất thép hồ quang làm cho thép có khả năng tái sử dụng gần như 100%.
a. Trình độ công nghệ
Về trình độ công nghệ, công nghệ EAF ở Việt Nam có thể chia thành 3 nhóm: nhóm công nghệ lạc hậu, nhóm công nghệ trung bình và nhóm công nghệ tiên tiến.
Các thông số chính để phân nhóm công nghệ bao gồm: dung lượng lò luyện, tiêu hao điện năng, tiêu hao điện cực, thời gian nấu luyện (bảng 1).
Bảng 1: Các thông số và khoảng giá trị phân nhóm công nghệ
(Nguồn: Báo cáo tổng kết Đề tài cấp Bộ “Nghiên cứu xây dựng lộ trình triển khai và áp dụng các tiêu chuẩn, qui định quản lý năng lượng, phát thải và sử dụng công nghệ sạch trong các ngành công nghiệp trọng điểm”. Hà Nội tháng 3/2015.)
b. Sử dụng năng lượng
Năng lượng sử dụng trong công nghệ EAF chủ yếu là điện năng. Ngoài ra còn có các loại năng lượng khác như than cám, oxy… Tổng các mức tiêu hao năng lượng của các nhóm công nghệ lò EAF (bảng 2).
Bảng 2: Tiêu hao năng lượng trong luyện thép theo công nghệ EAF
Ghi chú: (*)WBP (World Best Practice): Tiêu chuẩn thực hành tốt nhất thế giới
Do các nguồn thông tin không đầy đủ và một số thiếu tin cậy, nên số liệu trong bảng trên cũng chỉ là con số tương đối. Theo đó, so với WBP thì các nhóm công nghệ lạc hậu, trung bình và tiên tiến của các lò EAF của nước ta tiêu hao năng lượng cao hơn lần lượt là: 1,28; 1,12 và 1,056 lần.
Nói cách khác là nhóm các cơ sở luyện thép EAF tiên tiến của nước ta có công nghệ tương đương với quốc tế. Đối với các nhóm lạc hậu và trung bình thì tiềm năng tiết kiệm năng lượng còn rất lớn. Theo đánh giá của TS Nguyễn Văn Sưa (Hiệp hội Thép Việt Nam) trong báo cáo “Đánh giá thực trạng và nhu cầu sử dụng công nghệ sạch đối với ngành luyện thép, Báo cáo Chuyên đề, 12/2014”, thì tiềm năng tiết kiệm năng lượng của phân ngành luyện thép bằng công nghệ EAF ở Việt Nam có thể đạt từ 5,6% đến 28% so với thế giới.
Ngoài ra, đổi mới công nghệ, ứng dụng các công nghệ tiên tiến, công nghệ sạch hơn cũng là một vấn đề cấp bách của ngành thép Việt Nam trong bối cảnh hội nhập quốc tế toàn diện và sâu rộng hiện nay và trong những năm tới.
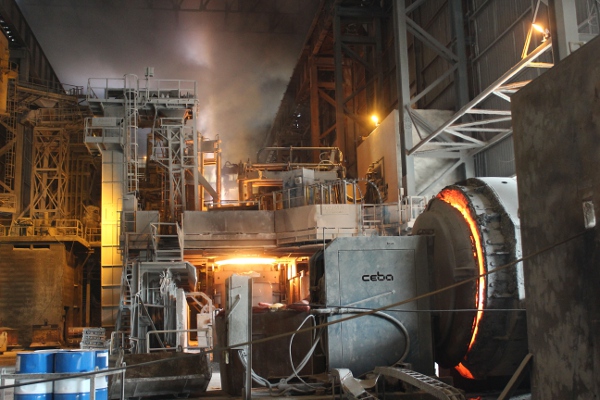
Công nghệ IF
Theo tài liệu của Hiệp hội Thép Việt Nam tại thời điểm 2014, Việt Nam có 38 lò IF với dung lượng lò từ 6 tấn/mẻ đến 50 tấn/mẻ. Tổng công suất thiết kế khoảng 2.400.000 tấn/năm. Sản lượng phôi thép năm 2017 của các nhà máy luyện thép bằng lò IF khoảng 800.000 tấn, chiếm khoảng 7% tổng sản lượng phôi thép của cả nước.
a. Trình độ công nghệ
Tất cả các lò IF luyện thép ở nước ta đều do Trung Quốc chế tạo. Hiện nay mới có rất ít nghiên cứu đánh giá về công nghệ này. Trên thế giới, lò cảm ứng luyện thép thông thường cũng mới chỉ được sử dụng nhiều ở Ấn Độ, Trung Quốc và gần đây là ở Việt Nam.
b. Sử dụng năng lượng
Hiện nay lò cảm ứng luyện thép chỉ sử dụng một loại năng lượng duy nhất là điện năng. Theo Báo cáo tổng kết đề tài “Đánh giá hiệu quả sản xuất phôi thép trong công nghệ luyện thép bằng lò cảm ứng”, tháng 12-2014 của TS. Nguyễn Văn Sưa, tiêu hao điện năng để sản xuất được 1 tấn phôi thép bằng lò IF ở nước ta nằm trong khoảng 600-800 kWh/tấn.
Nhìn chung, tiềm năng tiết kiệm năng lượng của các đơn vị sản xuất thép còn khá cao. Để giải quyết vấn đề tiết kiệm nguyên liệu, năng lượng và bảo vệ môi trường, ngành Thép cần có lộ trình đổi mới công nghệ và áp dụng công nghệ sạch.
Nhu cầu phát triển và định hướng lựa chọn công nghệ trong ngành thép
Theo dự báo (Quy hoạch phát triển hệ thống sản xuất và hệ thống phân phối thép giai đoạn đến 2020, có xét đến năm 2025) thì mục tiêu đến năm 2020 sản lượng gang và sắt xốp sẽ khoảng 13 triệu tấn; sản lượng phôi thép đạt 20 triệu tấn; sản lượng thép thành phẩm đạt khoảng 23 triệu tấn. Con số tương tự của năm 2025 là khoảng 18 - 20 triệu tấn gang và sắt xốp; 33 - 35 triệu tấn phôi thép và khoảng 39 triệu tấn thép thành phẩm.
Theo Hiệp hội Thép Việt Nam, để phát triển hệ thống sản xuất và phân phối thép giai đoạn đến 2020, có xét đến năm 2025 cần tập trung một số yêu cầu sau:
+ Ưu tiên đầu tư các dự án sản xuất gang, phôi thép, thép tấm cán nóng, thép hợp kim, thép chất lượng cao, thép hình cỡ lớn, thép không gỉ hiện nay trong nước sản xuất chưa đáp ứng đủ nhu cầu hoặc chưa sản xuất được;
+ Chỉ thực hiện đầu tư các dự án sản xuất gang, phôi thép từ quặng sắt trên địa bàn sau khi đã xác định được trữ lượng tin cậy của nguồn quặng sắt, đảm bảo có đủ nguồn nguyên liệu ổn định, lâu dài (tối thiểu là 15 năm) và đảm bảo hiệu quả kinh tế của Dự án. Đồng thời, khai thác nguồn than mỡ trong nước; nhập khẩu than mỡ, than cốc đáp ứng đủ cho nhu cầu trong nước;
+ Các dự án sản xuất thép theo công nghệ EAF tiêu thụ nhiều điện năng, do vậy, để đảm bảo đủ nguồn điện cung cấp cho dự án, trước khi cấp phép đầu tư, Chủ đầu tư cần có thoả thuận của ngành điện nơi đặt nhà máy luyện thép;
+ Áp dụng công nghệ tiên tiến, hiện đại với suất tiêu hao nguyên liệu, điện năng thấp, đảm bảo các yêu cầu về phát thải, thân thiện với môi trường, lắp đặt hệ thống quan trắc tự động đối với khí thải.
Đặc biệt, quy mô công suất thiết bị luyện kim phải đảm bảo các yêu cầu sau:
+ Công nghệ lò cao: Đối với khu vực không có nguồn quặng sắt tập trung, yêu cầu dung tích lò cao tối thiểu 500 m3 (không kể các lò cao chuyên dùng sản xuất gang đúc phục vụ ngành cơ khí); đối với khu vực có nguồn quặng sắt tập trung, yêu cầu dung tích lò cao tối thiểu 700 m3; đối với các dự án sử dụng quặng sắt nhập khẩu, bố trí tại khu vực ven biển, yêu cầu dung tích lò cao tối thiểu 1000 m3;
+ Công nghệ lò điện hồ quang EAF: công suất tối thiểu 70 tấn/mẻ;
+ Công nghệ lò thổi ôxy BOF: công suất tối thiểu 50 tấn/mẻ;
+ Dây chuyền cán thép: công suất tối thiểu 500.000 tấn/năm.
Đồng thời, tăng cường đầu tư dự án sản xuất gang, sắt xốp theo công nghệ luyện kim phi cốc. Từng bước nâng cấp, thay thế các nhà máy sản xuất nhỏ, công nghệ lạc hậu.
Đến năm 2020, cơ bản loại bỏ các nhà máy sản xuất gang, phôi thép, dây chuyền cán thép có công suất nhỏ (trừ lò cao sản xuất gang đúc phục vụ ngành cơ khí, lò chuyên dùng đúc chi tiết cơ khí, dây chuyền cán thép không gỉ và thép chất lượng cao).
Từ năm 2013 trở đi không cấp phép đầu tư cho các dự án mới có công nghệ lạc hậu, ô nhiễm môi trường, tiêu hao nhiều năng lượng. Các dự án đầu tư phải tuân thủ theo Quy chuẩn kỹ thuật quốc gia về công nghệ, thiết bị sản xuất gang, thép do Bộ Công Thương quy định.
Một số văn bản pháp luật liên quan: - Thông tư số 03/2014/TT-BCT quy định về công nghệ, thiết bị sản xuất gang thép: Thông tư này quy định về công nghệ, thiết bị đối với các cơ sở sản xuất gang, thép bao gồm luyện than cốc, thiêu kết, luyện gang, luyện thép lò chuyển, luyện thép lò điện hồ quang, luyện thép lò cảm ứng và cán thép. Căn cứ Thông tư này thì các nhà máy luyện gang bằng lò cao và luyện thép bằng lò điện hồ quang mới xây dựng phải có suất tiêu hao năng lượng lần lượt không được lớn hơn 14.000 MJ/T và 2.600 MJ/T. - Các Tiêu chuẩn, quy chuẩn đã ban hành: + Quy chuẩn QCVN 07: 2009/BTNMT - Quy chuẩn kỹ thuật quốc gia về ngưỡng chất thải nguy hại do Bộ Tài nguyên và Môi trường ban hành tại Thông tư số 25/2009/TT-BTNMT ngày 16/11/2009. + Quy chuẩn QCVN 51: 2013/BTNMT-Quy chuẩn kỹ thuật quốc gia về khí thải công nghiệp sản xuất thép + Quy chuẩn QCVN 51: 2013/BTNMT - Quy chuẩn kỹ thuật quốc gia về khí thải công nghiệp sản xuất thép được Bộ Tài nguyên và Môi trường ban hành tại Thông tư số 32/2013/TT-BTNMT ngày 25/10/2013. + Quy chuẩn QCVN 52: 2013/BTNMT - Quy chuẩn kỹ thuật quốc gia về nước thải công nghiệp sản xuất thép được Bộ Tài nguyên và Môi trường ban hành tại Thông tư số 32/2013/TT-BTNMT ngày 25102013. |
Ths. Phạm Văn Liêm - Hiệp hội Công nghiệp môi trường Việt Nam