Thép Hoà Phát ứng dụng kinh tế tuần hoàn tiết kiệm chi phí
Thứ hai, 20/09/2021
Tập đoàn Hoà phát đã đẩy mạnh mô hình kinh tế tuần hoàn trong nhiều hoạt động sản xuất - kinh doanh, giúp tiết giảm hàng nghìn tỷ đồng chi phí sản xuất - kinh doanh và gia tăng giá trị chuỗi sản xuất.
Mô hình kinh tế tuần hoàn đưa một phần hoặc toàn bộ chất thải về vòng sản xuất cũ, cấu trúc lại và sử dụng lại. Do đó góp phần giảm tiêu thụ nguyên liệu, thu hồi chất thải cho đầu vào sản xuất, giảm chi phí sản xuất và hướng đến sự phát triển bền vững. Tập đoàn Hoà phát đã đẩy mạnh mô hình kinh tế tuần hoàn trong nhiều hoạt động sản xuất - kinh doanh, giúp tiết giảm hàng nghìn tỷ đồng chi phí sản xuất - kinh doanh và gia tăng giá trị chuỗi sản xuất.
Tiết giảm chi phí hàng nghìn tỷ đồng nhờ mô hình kinh tế tuần hoàn
Với đặc thù sản xuất công nghiệp đa ngành, đa lĩnh vực, trong đó hoạt động sản xuất gang thép sử dụng lượng lớn điện, nước, than… Tập đoàn Hoà Phát đã áp dụng mô hình kinh tế tuần hoàn vào quá trình sản xuất kinh doanh nhằm sử dụng tiết kiệm các loại năng lượng, tài nguyền thiên nhiên, góp phần bảo vệ môi trường.
Tập đoàn Hoà Phát đã xây dựng thành công công nghệ lò cao liên động khép kín từ quặng sắt đến thép thành phẩm, hay còn gọi là sản xuất thép từ thượng nguồn tại Việt Nam. Cả hai khu liên hợp sản xuất gang thép Hải Dương và Dung Quất của Hoà Phát đều là những tổ hợp khép kín, gồm Nhà máy Chế biến nguyên liệu, Nhà máy Sản xuất than coke và nhiệt điện, Nhà máy Luyện gang, Nhà máy Luyện thép đến Nhà máy Cán thép và các đơn vị phụ trợ khác.
Trong đó, sản phẩm của nhà máy này lại là nguyên liệu đầu vào của nhà máy kia nhằm tối ưu hoá chuỗi giá trị gia tăng của chu trình luyện kim. Đồng thời, việc khép kín chuỗi sản xuất còn giúp các nhà máy thu hồi triệt để và tái sử dụng hiệu quả khí thải, nước thải, nhiệt dư cũng như chất thải rắn sau mỗi công đoạn sản xuất.
Trong khâu luyện thép, Tập đoàn Hoà Phát sử dụng công nghệ lò thổi oxy (BOF) với mức tiêu thụ điện thấp hơn từ 10% - 15%/tấn thép so với công nghệ lò điện (EAF) đang được sử dụng phổ biến tại Việt Nam. Tuy nhiên, công nghệ BOF sinh ra một lượng lớn khí CO độc hại, dễ cháy.
Để giải quyết vấn đề này, hệ thống sản xuất đã được các kỹ sư Hoà Phát cải tiến nhằm thu hồi triệt để toàn bộ lượng khí CO, tích trữ trong bồn chứa dung tích lớn nhằm tái sử dụng làm nhiên liệu đốt thay vì sử dụng nhiên liệu LPG hay dầu FO trong các công đoạn sản xuất khác như nung vôi làm phụ gia tạo xỉ, sản xuất quặng vê viên (pellet)…
Bên cạnh đó, lượng hơi nước quá nhiệt có nhiệt độ trên 150oC - 200oC và áp lực 6.5 bar sinh ra từ quá trình luyện thép và cán thép lại được tận dụng, dẫn ngược về phục vụ các công đoạn sản xuất khấc như thiêu kết và sản xuất pellet. Đồng thời, áp lực hơi nước được giảm xuống còn 4 bar để phục vụ bếp ăn của các khu liên hợp, thay thế cho việc sử dụng khí đốt. Giải pháp tận dụng hơi quá nhiệt này giúp tiết giảm hơn 200 triệu đồng/tháng chi phí sử dụng khí gas tại các bếp ăn.
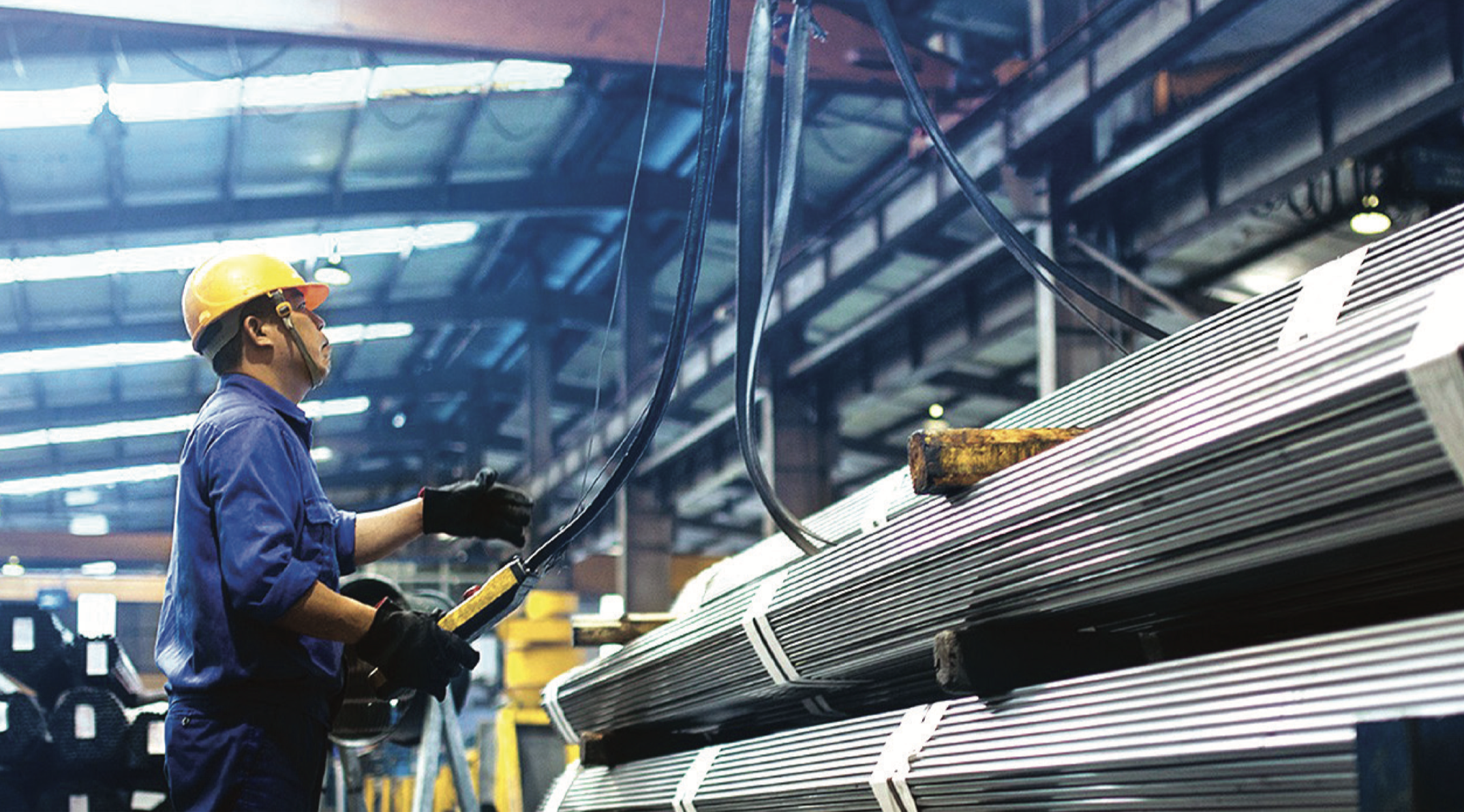
Việc áp dụng mô hình kinh tế tuần hoàn đã giúp tập đoàn Hoà Phát tiết kiệm hàng nghìn tỷ đồng chi phí sản xuất kinh doanh cũng như gia tăng đáng kể giá trị chuỗi sản xuất thép.
Một cải tiến khác là hầu hết các lò gia nhiệt phôi thép thường được đốt bằng dầu FO thì Khu Liên hợp gang thép Hải Dương lại sử dụng hệ thống 10 lò khí hóa than để sản xuất khí CO từ than anthracite làm nhiên liệu cung cấp cho các lò gia nhiệt của các nhà máy cán, tiết kiệm đến 50% chi phí nhiên liệu cho công đoạn cán thép. Lượng bụi chứa sắt thu hồi được trong quá trình luyện gang thép, cán thép cũng đều được tái sử dụng ở các công đoạn sản xuất; đồng thời, giúp tăng tuổi thọ của dây chuyền sản xuất.
Việc luyện than cốc cũng được Tập đoàn Hoà Phát lựa chọn công nghệ dập cốc khô bằng khí N2 tiên tiến thay vì công nghệ nhiệt phân than mỡ kiểu truyền thống. Công nghệ dập cốc khô bằng khí N2 giúp giảm thiểu việc thải ra các sản phẩm phụ như dầu coke, dầu nhẹ, hắc ín… vốn gây ô nhiễm nặng nền không khí và nguồn nước.
Công nghệ dập than cốc tiên tiến này cũng cho phép thu hồi lượng nhiệt dư để sản xuất điện. Khu liên hợp gang thép Hải Dương đã đưa vào vận hành 4 tổ máy phát điện nhiệt dư với tổng công suất thiết kế 60 MW, cung cấp khoảng 1/3 lượng điện tiêu thụ của toàn khu Liên hợp. Nếu tính theo giá điện công nghiệp trung bình hiện tại, mức tiết kiệm chi phí điện năng từ giải pháp này lên đến 40,3 tỷ đồng/tháng.
Còn tại Khu Liên hợp gang thép Dung Quất, chi phí tiết kiệm được nhờ các giải pháp trên thậm chí còn cao hơn khoảng 2,5 lần so với ở Hải Dương, do quy mô sản xuất lớn hơn, hệ thống tối ưu và hiện đại hơn. Năm 2020, khu liên hợp này sử dụng gần 1,6 tỷ KWh điện năng, trong đó 1,2 tỷ KWh do khu liên hợp tự sản xuất được (đạt mức tự chủ 80%). Tính một cách tương đối, chi phí tiết kiệm được nhờ giải pháp thu hồi nhiệt, khí thải ở các khu liên hợp thép của Hòa Phát từ năm 2021 trở đi nằm trong khoảng 4.000 tỷ đồng.
Tận dụng phế phẩm mở rộng hệ sinh thái sản phẩm
Trong quá trình sản xuất thép, Tập đoàn Hoà Phát đã triển khai thu gom, chế biến xỉ lò cao – chất thải rắn trong quá trình luyện gang để biến thành sản phẩm mới cho ngành Xây dựng. Nhờ được làm lạnh cực nhanh bằng nước áp lực cao, xỉ hạt lò cao từ các khu liên hợp gang thép của Tập đoàn Hoà Phát có hoạt tính cao, phù hợp cho sản xuất xi măng, bê tông, vữa hoặc làm chất kết dính gia cố nền đất yếu.
Xỉ hạt lò cao của Hoà Phát còn được dùng để sản xuất được bê tông khối lớn do giảm nhiệt thủy hóa của bê tông, sản xuất được bê tông chịu nhiệt do tăng độ bền nhiệt cho bê tông, sản xuất bê tông bền trong môi trường nước biển, nước mặn và nước lợ, do tăng độ chống thấm của bê tông, ngăn chặn sự xâm thực của clo và sulfate, đáp ứng nhu cầu tăng tuổi thọ cho các công trình trên biển, trên đảo và ven biển.
Đặc biệt, sản phẩm này sẽ giúp hạ giá thành bê tông thương phẩm do xỉ hạt lò cao có chi phí thấp, giảm hàm lượng clinker trong xi măng, nhờ đó làm giảm lượng khí CO2 phát thải. Việc tận dụng xỉ hạt lò cao nghiền mịn đã góp phần xử lý triệt để chất thải rắn trong quá trình sản xuất gang thép của Hòa Phát, vừa bảo vệ môi trường cũng như tạo thêm nguồn thu ổn định cho doanh nghiệp, đem lại giá trị gia tăng đáng kể cho chuỗi sản xuất thép.
Văn phòng SX&TDBV