Ngành xi măng đẩy mạnh tận dụng nhiệt thừa, rác thải
Thứ sáu, 15/03/2019
Là ngành tiêu thụ nhiều điện và than, trong khi giá điện, than được dự báo sẽ tiếp tục tăng trong năm 2019 buộc các doanh nghiệp ngành xi măng phải tính đến tiết kiệm điện năng như tận dụng nhiệt thừa hay đốt rác thải để phát điện; gia tăng tỷ lệ sử dụng tro bay…
Là ngành tiêu thụ nhiều điện và than, trong khi giá điện, than được dự báo sẽ tiếp tục tăng trong năm 2019 buộc các doanh nghiệp ngành xi măng phải tính đến tiết kiệm điện năng như tận dụng nhiệt thừa hay đốt rác thải để phát điện; gia tăng tỷ lệ sử dụng tro bay…
Một lãnh đạo doanh nghiệp ngành xi măng cho biết, trước giá điện “mềm” hơn thì dự án tận dụng nhiệt thừa hay đốt rác thải chưa được doanh nghiệp quan tâm. Nếu tính đến hiệu quả sử dụng đồng vốn thì đầu tư hệ thống tận dụng nhiệt thừa chưa thực sự hiệu quả cao. Nhưng khi giá điện tiếp tục tăng thì doanh nghiệp buộc phải tính toán cân đối để làm.
Nhiều doanh nghiệp xi măng lớn trên thế giới sử dụng 10 - 17% nhiên liệu thay thế phục vụ sản xuất. Đi đầu trong ứng dụng công nghệ tận dụng nhiệt thừa để phát điện phải kể đến Holcim Việt Nam và VICEM. Holcim Việt Nam đã sử dụng nguồn nhiên liệu thay thế (là rác thải có thể đốt được, phế thải nhựa, dầu thải cùng các loại phế thải ngành công nghiệp giày dép - may mặc) lên đến 14%.
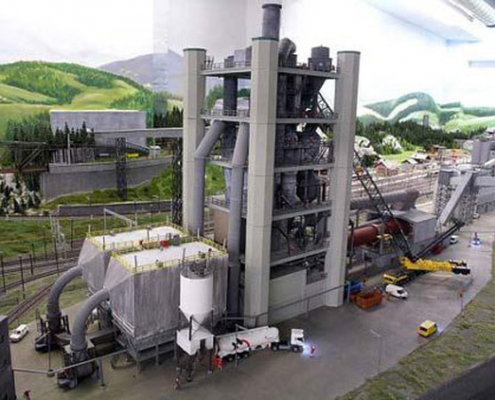
Theo Tổng Giám đốc VICEM Bùi Hồng Minh, VICEM đang nghiên cứu triển khai dự án thu hồi nhiệt khí thải và thử nghiệm đốt rác để bảo vệ môi trường. Trạm nghiền Bình Phước đang thử nghiệm đốt rác trực tiếp. Sau khi hoàn thành thử nghiệm sẽ nghiên cứu triển khai rộng rãi, DN sẽ chủ động hơn trong sản xuất vì có nguồn nhiên liệu ổn định, lâu dài.
Các chuyên gia khuyến cáo, do giá than tăng nên trong thời gian tới, thay vì sử dụng 100% nhiên liệu than, các doanh nghiệp xi măng Việt Nam cần sớm chuyển sang sử dụng nguồn nhiên liệu thay thế để giảm chi phí sản xuất. Để ngành xi măng phát triển bền vững hơn, sản xuất xanh - sạch hơn thì bài toán về môi trường cũng cần đặt nặng lên đôi vai doanh nghiệp xi măng thay vì chỉ có bài toán kinh tế.
Áp lực với ngành xi măng giai đoạn này là cả nước hiện có 29 dây chuyền công suất từ 250.000 - 600.000 tấn/năm, với tổng công suất 11,49 triệu tấn, chiếm 11,76% tổng công suất thiết kế. Đây là những dây chuyền đã đầu tư trên 15 năm, thiết bị lạc hậu, tiêu hao nhiều nguyên, nhiên liệu, dẫn đến giá thành tăng, sức cạnh tranh thấp, thậm chí một số nhà máy phải mua clinker để nghiền xi măng. Có 13 dây chuyền công suất 910 nghìn tấn/năm, với tổng công suất 11,83 triệu tấn, chiếm 12,12% tổng công suất thiết kế. Mặc dù các dây chuyền này có công nghệ tiên tiến nhưng chi phí sản xuất vẫn cao do tiêu hao nhiên liệu lớn, sức cạnh tranh thấp.
Một quy luật tất yếu của thị trường là trong giai đoạn cạnh tranh toàn diện về chất lượng - dịch vụ - giá cả thì những dây chuyền công suất nhỏ, chi phí lớn, giá thành cao sẽ khó có khả năng cạnh tranh trên thị trường, khó tiêu thụ sản phẩm. Sẽ đến giai đoạn đào thải, những dây chuyền xi măng quy mô nhỏ sẽ phải tự động dừng sản xuất vì không thể cạnh tranh nổi.
Theo đúng quy luật thị trường xi măng thế giới, để tiết giảm chi phí, tăng tính cạnh tranh, nâng cao chất lượng sản phẩm, ngành xi măng Việt Nam sẽ hình thành các tập đoàn, doanh nghiệp xi măng lớn, công nghệ hiện đại. Xi măng Việt Nam hiện có 10 dây chuyền lớn công suất từ 2,3 triệu tấn/năm trở lên, với tổng công suất 26,2 triệu tấn, chiếm 26,83% tổng công suất thiết kế, là dây chuyền có công nghệ hiện đại trên thế giới hiện nay; tiêu hao nguyên, nhiên liệu thấp và đã đầu tư lắp đồng bộ hệ thống tận dụng nhiệt khí thải lò nung để phát điện, tiết kiệm được 20 - 30% tổng lượng điện sử dụng.
Theo ximang.vn